Ответ прост — сделать так, чтобы оно не ломалось.Но сейчас, когда ситуация изменилась, возникают дополнительные сложности:
Проблемы с поставками
Рост цен на комплектующие
Невозможность купить запчасти
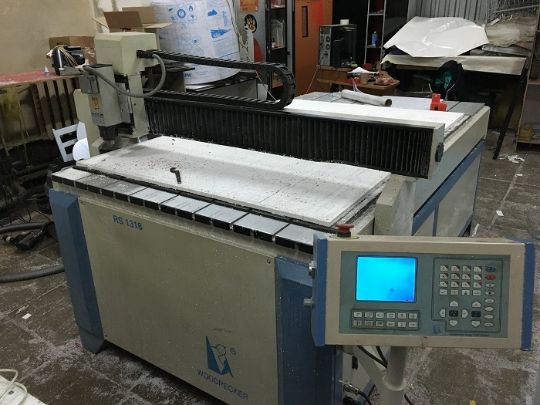
Поставки импорта стали либо полностью недоступны, либо осуществляются сложным маршрутам. В результате сроки обеспечения запасными частями становятся непредсказуемыми, откладывается плановое и аварийное техническое обслуживание оборудования, растут риски для бизнеса.
Сложные и уникальные станки в ближайшем будущем могут стать грудой железа, потому что автоматизированная система просто не примет “не родной” сервомотор.
Сложные и уникальные станки в ближайшем будущем могут стать грудой железа, потому что автоматизированная система просто не примет “не родной” сервомотор.
Да, можно попытаться найти замену в том же Китае. Но это большие временные и финансовые затраты на поиск аналогов, закупке, тестированию и так далее.
Чем грозит простой оборудования?
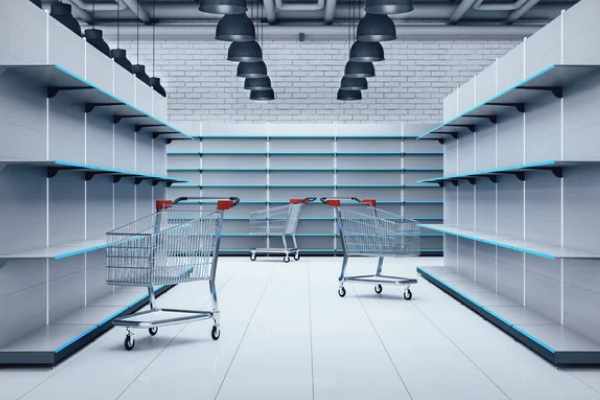
Недовыпуск продукции
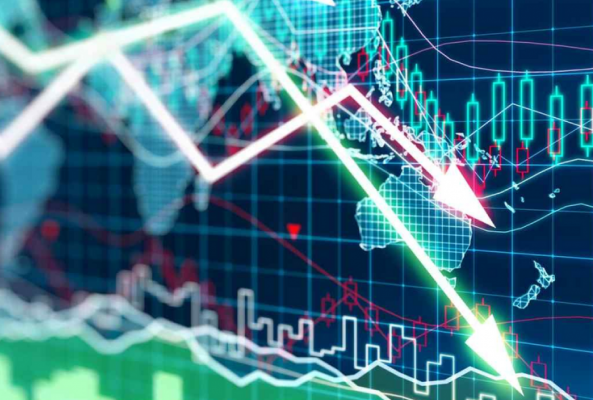
Потеря выручки
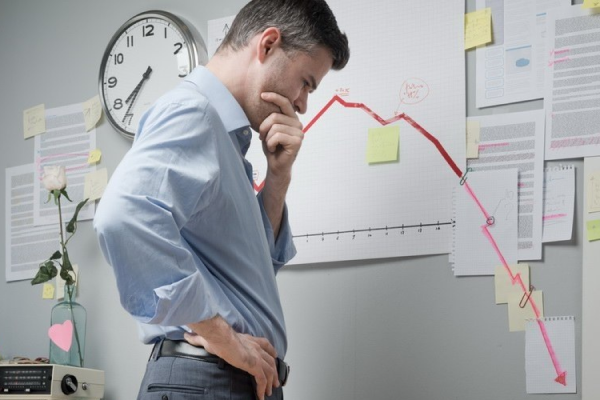
Потеря клиентов
Выход есть
Нужно работать над тем, чтобы оборудование прослужило, как можно дольше. Сделать это можно за счет повышения надежности оборудования.
Как это сделать?
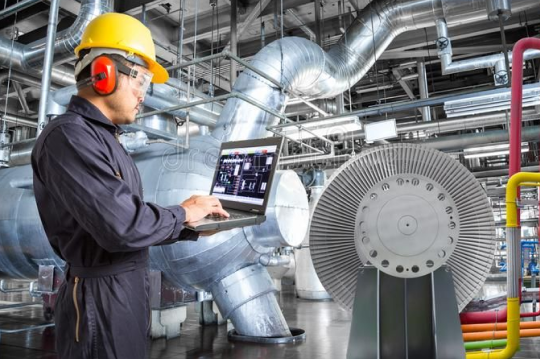
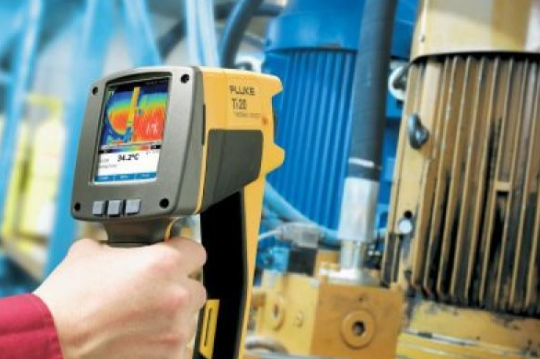
Прежде всего, необходимо увеличить межремонтный цикл оборудования. Это значит, что самое время “ставить” систему прогнозирования поломок.
Важно сосредоточить усилия на своевременной и качественной диагностике, чтобы понимать текущее состояние оборудования и риски, чтобы уметь вовремя поставить тот самый “костыль”, пока логисты и инженеры решают вопросы замены и подбора аналогов на запчасти.
Достигается это не только с помощью использования сложного диагностического оборудования, но в том числе и с помощью грамотных обходов и осмотров силами специалистов.
Сейчас не время экономить на персонале, наоборот, самое время усилить подготовку и обучение, передачу навыков от опытных специалистов менее квалифицированным, создавать стандарты, быстро запускать системы осмотров и обходов, анализировать данные о проблемах оперативно и оперативно устранять первопричины проблем.
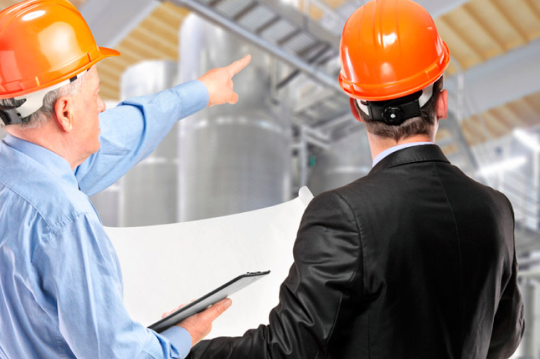
Только за последние 2 года мы работали с тремя компаниями, где такие системы приходилось либо ставить с нуля, либо серьезно менять большинство процессов.
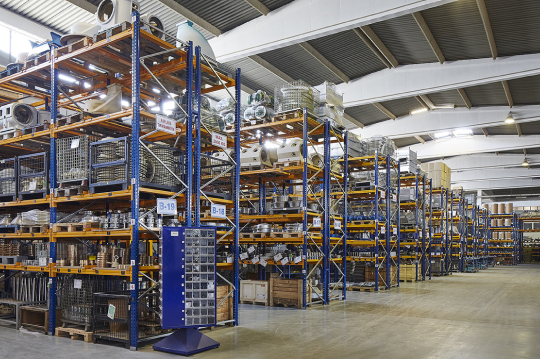
Кроме того, очень важно сейчас навести порядок на складах запасных частей и расходных материалов. Разобрать залежи запасов, накопленных в тучные времена. В 80% случаях фактическая номенклатура остатков (годами складируемых у ремонтников) имеет отклонения по отношению к бухгалтерским отчётам, а списание запасных частей не всегда проводится в привязке к конкретным работам ТО, что затрудняет учёт и планирование.
В условиях неопределенности не время рассчитывать запас по формулам, но важно создать прозрачную и работающую систему учета запасных частей.
Можно ли это сделать самостоятельно? Можно, но если делать это путем проб и ошибок, на это уйдет колоссальное количество времени и ресурсов.
Гораздо эффективнее и стратегически правильнее делегировать эту задачу консалтинговой компании.
Командой “Топ Менеджмент Консалт” помимо внедрения Бережливого производства и 6 Сигма, специализируется на проектах по внедрению систем надежности оборудования. У нас обширный опыт: за более чем 22 года мы поработали с производственными и научными предприятиями из самых разных сфер: золотодобыча, нефтегазовый сектор, инженерные компании, IT-компании и не только.
КАК МЫ ВНЕДРЯЕМ
Сессии по Надежности оборудования
Мы готовы провести очную сессию для ведущих специалистов и руководства компании, чтобы подробно рассказать о преимуществах внедрения системы надежности оборудования.
В ходе сессии мы расскажем о вариантах внедрения, способах контроля достижения результата и эффекте от внедрения.
Подобные сессии решают не только задачи по информированию компании, но и значительно повышают вовлеченность сотрудников, что в конечном счете в разы повышает эффективность внедрения.
Работаем по KPI
В ходе разработки дорожной карты внедрения надежности оборудования мы не только указываем основные инструменты, с помощью которых мы добьемся результата, и сроки, в которые этот результат будет достигнут, но и определяем ключевые показатели эффективности (KPI), которые мы также будем контролировать в ходе внедрения.
Частые вопросы по TPM
Сколько внедряется?
Полгода - базис. В течение 2-3 лет внедряются принципы и технологии, которые позволяют бизнесу почувствовать эффект.
Участники внедрения?
Участвуют все кадры.
Как происходит внедрение?
Поиск первопричин с помощью разных методов. Далее фиксируются первопричины, ее купирование и принятие временного решения. Затем применяется более постоянное решение, которое призвано показать не только результат, но и устойчивость этого решения.
С НАМИ РАБОТАЮТ
ОСТАЛИСЬ ВОПРОСЫ?
© ТОП-МЕНЕДЖМЕНТ КОНСАЛТ. 1999-2022